Exploring Varieties and Design Features of Rotary Shaft Seals
Nov 09, 2023 Material | LIP Seals | Mechanical Seals
The performance of most industrial processes depends on various scalar and vector quantities such as motion, speed, force, and more, which are based on direction, magnitude, or both. All of these quantities together facilitate the working of any machine or equipment in terms of mobility, movement in a particular direction, and so on. Some of them demand oscillating movements, hydraulics, and continuous rotation to get the desired outcomes. Here, the biggest challenge is that the equipment or machine that oscillates or rotates should be well connected to the fixed portions, well-lubricated, and not cause friction. Additionally, with continuous usage, these parts may get exposed to environmental parameters, such as dust and moisture, which must be prevented. Rotary shaft seals make a significant difference here. Popularly called rotary shaft oil seals, they are used to seal lubrication fluids in these parts, thus increasing their operational life and contributing to the system's overall performance. Today, different types of rotary shaft seals are available in the market. Each is differentiated based on its design characteristics. Are you intrigued to know more about them? If yes, then read this post till the end.
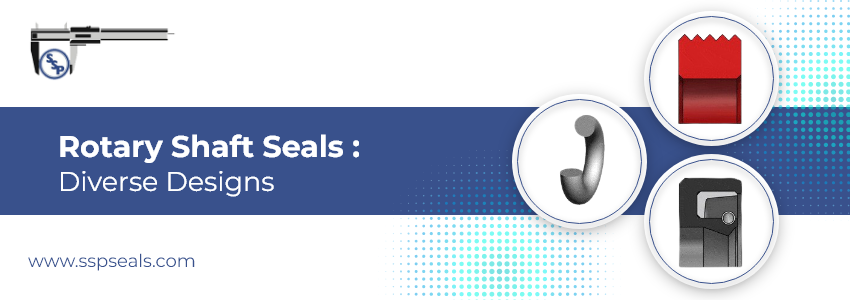
Understanding Rotary Shaft Seal Types and Their Distinct Design Characteristics
Here are some common types of rotary shaft seals with their design characteristics.
- Radial Lip Seals: These are the most commonly used rotary shaft seals. As the name suggests, they feature a flexible elastomer lip that contacts the shaft. This helps in creating a dynamic sealing interface. Here are some key design characteristics of these seals.
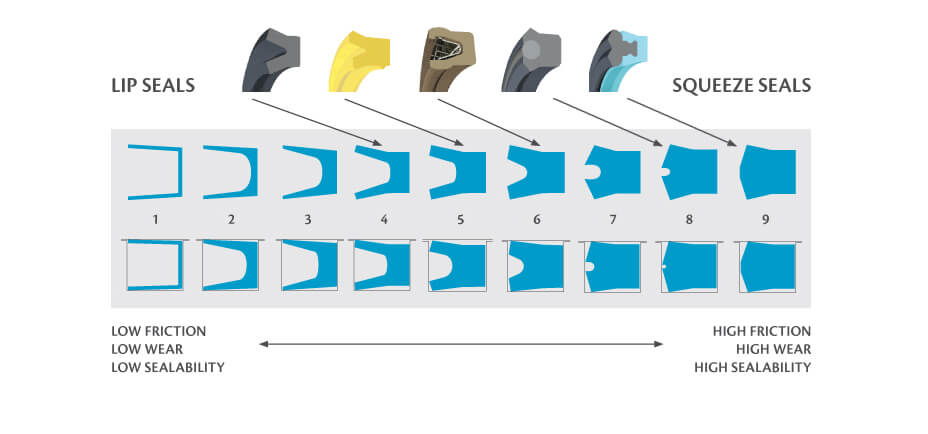
- Lip Geometry: The lip design can vary depending on the application requirements. Single lips, double lips, and even triple lips are popular options for enhanced sealing performance.
- Spring-Loaded: Many lip seals comprise a spring to ensure constant lip-to-shaft contact, even when there are variations in shaft speed.
- Materials: They are made using materials such as nitrile rubber, Viton, silicone, and polyurethane. The material selection depends on factors such as fluid compatibility, temperature, and chemical resistance.
- Lubrication Grooves: Most lip seals have lubrication grooves on the sealing lip. This maintains a thin layer of lubricant between the lip and the shaft.
- Mechanical Seals: They find application where leakage control and high performance are paramount. The design characteristics of mechanical seals are as follows.
- Materials: They are made from materials such as ceramic, silicon carbide, carbon, and various elastomers. These materials offer great resistance to heat, wear, and chemical corrosion.
- Stationary and Rotating Components: They consist of stationary and rotating components engineered to create a seal that can withstand high pressures and temperatures.
- Leakage Control: Their robust design and precise manufacturing provide superior control over leakage.
- Applications: These seals are commonly used in compressors, pumps, and other high-performance machinery.
- Magnetic Seals: They are designed especially for high-speed and high-temperature applications. Here are the design characteristics of magnetic seals.
- High-Speed Capability: They are ideal for high-speed applications such as centrifugal pumps, turbochargers, and more.
- Hermetic Sealing: They provide hermetic sealing, preventing any contamination or leakage.
- Magnetic Coupling: These seals use the principle of magnetic coupling to create a seal without physical contact between the seal and the shaft.
- Low on Maintenance: The maintenance cost of these seals is minimal, reducing the need for regular replacements or servicing.
- Labyrinth Seals: As the name suggests, these seals have multiple barriers or labyrinths, thus the name. They use a series of intricate paths or channels to deter contaminants and fluids. They don’t create direct physical contact between the seal and the shaft. Here are some key design characteristics of labyrinth seals.
- Multiple Barriers: They have multiple barriers that create tortuous paths. These paths prevent the ingress of contaminants.
- Air or Gas Barrier: They can prevent the passage of air or gas, making them suitable for applications like rotating equipment in power plants.
- Minimal Friction: They introduce minimal friction in the system as there is no direct contact between the seal and the shaft.
- V-Ring Seals: These seals have a V-shaped cross-section, thus named. This cross-section allows them to confirm the shaft's surface, providing a secure seal. They are self-centering, and auto adjust to changes in the shaft position, which makes these seals a versatile and reliable option in various applications. Here are some design characteristics.
- V-Shaped Cross-Section: The V-shaped cross-section of the seal provides effective sealing while accommodating shaft runout.
- Self-Centering: These seals are self-centering. It means they adjust automatically to the changes in shaft position.
- Low Pressure Sealing: They are ideal for low to moderate pressure sealing applications.
- Wide Range of Sizes: V-ring seals are available in different sizes, making them adaptable to shaft dimensions.
- Hydraulic Seals: They are crucial components in hydraulic and pneumatic systems. They can prevent the escape of hydraulic fluids while simultaneously avoiding the entry of contaminants like dust and moisture. Here are some key design considerations of these seals.
- Materials: They are made using materials such as nitrile rubber, PTFE, polyurethane, and more. These materials are chosen for their ability to endure challenging operating conditions and compatibility with hydraulic fluids.
- Pressure and Temperature Resistance: They are designed to withstand high pressures and temperature variations, which is common in hydraulic systems.
- Lip and Wiper Seals: These seals include sealing lips to prevent fluid leakage and wiper seals to remove contaminants from the shaft.
- Cartridge Seals: These specialized sealing solutions find several industrial applications. They are designed to simplify installation, maintenance, and replacement processes. These seals are known for providing high performance for industrial pumps and similar equipment, where reliability and ease of maintenance are paramount. Here are some design characteristics of these seals.
- Self-Contained Unit: Cartridge seals come as a self-contained unit with all the necessary components for sealing.
- Easy Installation: They are easy to install, making them a preferred choice for applications where rapid maintenance is crucial.
- Reduced Downtime: They reduce downtime during seal replacement or servicing.

Are you an OEM that requires rotary shaft seals for rotating equipment? If yes, consult a reliable industry player like SSP Seals. The company is one of the most
trustworthy and experienced rotary shaft seal manufacturers that can cater well to your requirements. With close to 30 years of industry experience, the company offers a wide range of
seals and gaskets. This is possible because of their well-equipped facility, R&D, field support, customer service, and more. The company also offers custom rotary shaft seals depending on the application requirements. If you have any queries regarding rotary shaft seals, feel free to
contact their team.
Related Post