How to Choose the Best O-Ring for Your FDA Applications
Oct 03, 2023 Materials | FDA O-Rings | PTFE | Silicone
O-rings are resilient seals used in various applications across food and drug manufacturing, and packaging applications. These rings are used in valves, pumps, and other manufacturing equipment, where they create effective sealing. They ensure leak-free connections and prevent contamination, which are mandated by the
Food and Drug Administration (FDA). Although O-rings for the food and drug manufacturing industry may look similar to regular industries, they differ in terms of their construction, utility, and other factors. Being one of the highly regulated industries, the manufacturers operating in the food and pharmaceutical industries understand the importance of investing in FDA O-rings for food and drug manufacturing applications. There is an abundance of variety when it comes to FDA O-rings. However, not all rings are made the same. Choosing the perfect O-ring for FDA applications becomes challenging. This post aims to ease the selection process.
6 Important Tips to Choose FDA O-rings for Food and Drug Manufacturing Applications
Safety and sanitation requirements of the food and drug manufacturing industry differ from any regular industry. So, your selection process will be influenced by these requirements and other factors. The following are eight essential factors that you need to address when choosing FDA O-rings for dynamic applications for food and drug manufacturing facilities.
- Application Requirements: Every food and beverage processing or pharmaceutical manufacturing plant uses various types of chemicals, oils, and flavors. In addition to this, there are several equipment involved across the supply chain. So, you must have knowledge about the fluids, chemicals, or oils that the O-ring will come into contact with. In addition to this, you must address the operating conditions of your system, such as the maximum pressures and temperatures your system may be exposed to and so on.
- Material Selection: Choose a material that meets the FDA approval for food contact. A few common materials for food contact include:
- Silicone Rubber: This material is known for its low compression set characteristics and flexibility retention. It can be operated across the widest temperature range.
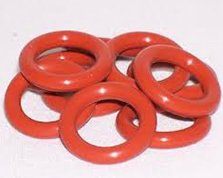
- Nitrile Rubber: This material maintains its flexibility at low temperatures and is known for its low compression set, high tensile strength, and high abrasion resistance. They are able to withstand temperatures ranging from -40°F to +257°F.
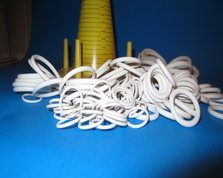
- Ethylene Propylene Diene Monomer (EPDM) Rubber: This material is durable, exhibits low compression set, and can resist chemicals, such as dilute solvents, alkalis, and certain solvents. It can be operated across a temperature range from -60°F to 300°F. These O-rings are ideal for applications involving extreme temperatures.
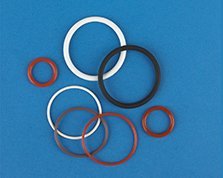
- PTFE (polytetrafluoroethylene): These O-rings offer excellent heat resistance and temperatures up to 350°F with any performance loss. PTFE O-rings are ideal for medium-pressure to low-pressure applications.
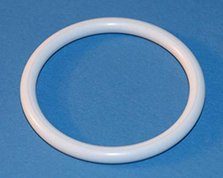
- Fluoroelastomers (e.g., Viton): Viton can withstand temperatures ranging from -13°F to 446°F and offer swell resistance from oxygenated fuel and high octane blends. These O-rings are not recommended for amines, ketones, nitro hydrocarbons, Skydrol® fluids, and so on.
- Pressure Resistance: Determine the range of pressures that an O-ring can withstand. It is essential as it ensures the O-ring doesn't extrude or fail under high-pressure conditions. The pressure resistance helps maintain the seal integrity, prevent seal failure and extrusion, ensure system reliability, address safety considerations, and promote longevity and cost savings.
- Size and Dimensions: It is essential to measure the O-ring's inner diameter (ID), outer diameter (OD), and cross-sectional diameter (CS). In addition to this, you must also measure the groove's dimensions before the O-ring is placed in it. This helps avoid leaks or mitigate inefficiencies. The O-ring needs to fit firmly inside the groove to create a reliable seal.
- Hardness and Durometer: O-rings are available in different hardness levels, typically measured using the Shore A or Shore D scales. Hardness determines the O-ring's resistance to deformation under pressure. Choosing the correct hardness and durometer helps ensure proper sealing performance, durability, and overall functionality of the O-rings. Therefore it is important to select the appropriate hardness level based on the application's specific needs.

- Source from Reputable Suppliers: Ultimately, it is one of the most prominent factors to choose a reliable and reputable O-ring supplier with a proven track record of producing high-quality products. A trustworthy supplier will provide technical support and guidance in selecting the right O-ring for your application. If they are responsive to customer inquiries, provide prompt assistance, and address any concerns or issues that may arise, you can select them without any second thought to achieve enhanced performance and overall satisfaction.

Selecting the perfect O-ring involves a systematic approach, considering various factors. By following the steps outlined above, you can source these O-rings from a reputable manufacturer like SSP Seals. The company provides custom FDA O-rings for dynamic applications in various materials, such as virgin PTFE, Polyurethane, EPDM, Silicone and Viton. They are used in filling equipment, tablet presses, cappers, bulk liquid transfer, centrifuges, packaging machines, and pumps. If you have any questions about FDA O-rings for food and drug application, please get in touch with the experts at SSP Seal and they will help you choose the material that best suits your needs.
Related Post