Industrial Seals and Gaskets; Major Types and Uses Explained
Oct 19, 2022 Industrial seals | Oil Seals | Gaskets | Rod Seals | LIP Seals
Industrial seals and gaskets are the terms that are generally used interchangeably as they perform similar functions in preventing leaks in applications. However, there are some key differences between the two that many users are unaware of. Since both seals and gaskets find immense applications in several industrial equipment and machinery, it imperative to understand their main differences along with their major types. Read on this post to know about seals & gaskets for industrial applications along with their major types.
What are Seals?
Seals are generally molded or machined products used in more active environments like engine parts, pumps and shafts, among others. They are designed in flat and round configurations to prevent the intrusion of particles and contaminants into systems. Manufactured from quality materials like Buna ‘N’ (Nitrile), CSR (Hypalon®), EPDM, Flourosilicone, Polyisoprene, Neoprene, Polyurethane, Silicone, and Viton®, industrial seals optimize the performance of different machines. A few popular types of seals include:
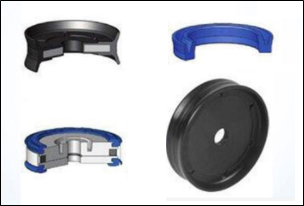
Maintaining the shelf life of your industrial seals can be tricky. Most times, industrial users purchase seals in bulk and store them for later use. In case the storage is not proper, it will drastically affect the performance and shelf life when put for industrial seals for applications later. The following are a few simple tips for storing your seals in order to maintain their quality whilst preventing spoilage.
- Oil Seals: Oil seals are rotary shaft seals that close the space between a stationary and a moving part to exclude dust, dirt, water or other contaminants. These types of seals find great deal of usage in gearboxes, pumps, gas and aircraft turbines and compressors. pistons, pipe connections, and hydraulic cylinders.
- Rod Seals: Capable of handling high pressure spikes, rod seals prevent leakage of hydraulic fluid outside the sealing system. They are available as single-acting and double acting seals and work best for linear and reciprocating dynamic sealing applications. Rod seals are one of the crucial elements in fluid power systems.
- Piston Seals: Piston seals, both single- and double-acting, prevent leakage of hydraulic fluid or air in industrial machinery, hydraulic and pneumatic cylinders and valves. Designed to provide ultimate leakage control, rod seals are used in extreme operating conditions.
- U-Cups Seals: As the name implies, these seals are available in different U-Cup configurations. Designed for both dynamic and static applications, they provide optimal sealing performance in pneumatic cylinders, off-road and construction vehicles and pneumatic- and hydraulic-powered equipment of all types.
- Lip Seals: Offered in various designs from single lip seal to multiple lip cartridge versions, lip seals prevent the ingress of water and dirt, while retaining lubricants. Owing to their outstanding resistance to wear, they can be used in demanding rotary situations including ships, water pumps and tidal turbines, pumps or gearboxes, water pumps and tidal turbines.
What are Gaskets?
Gaskets are mechanical pieces that are designed to create a static sealing between two non-moving items. Gaskets come in different designs to effectively seal two components or flanges by filling the gap between static mating surfaces. They are usually made from rubber, plastic, metal, and other materials such that they can withstand abrasion, vibration, impact, and temperature extremes. The following are the common types of gaskets used in various industrial applications.
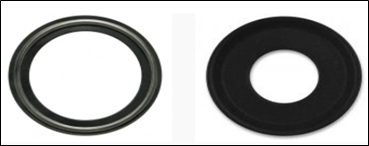
- Ring Gaskets: These are high integrity sealing solutions designed to create a tight and efficient sealing in raised or flat face flanges. Available in both oval and octagonal configurations, these gaskets are rightly suitable for high pressure and high temperature applications.
- Boiler Gaskets: Manufactured using high-grade raw materials in adherence to international quality standards, these gaskets contribute greatly to the system’s performance, uptime, and safety. Boiler gaskets are specifically designed to seal steam pressure vessels, hot water heaters, steam humidifiers, and water towers, among others.
- Tadpole Gaskets: Designed to provide a high temperature thermal seal, Tadpole gaskets are known for their ease of integration into component joints and seams. Manufactured from 304 stainless steel, Inconel®, fiberglass (Tetraglas®), silica, basalt, and ceramic, they are best suitable for small lab ovens, large industrial boilers and furnaces.
- Full Face Gaskets: Typically designed to use in flat faced flanges, these gaskets aid in sealing and protecting two separate pipe flanges. They cover the entire face of the flange and are better at stopping dirt from getting into the joints.
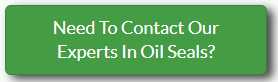
Despite the industrial seals and gaskets aforementioned, there are several more varieties of sealing products available in the market. Each has its own specific design, features and uses. Hence, selecting the most appropriate one holds a great significance. Associating with experienced and prominent seal manufacturer is the best way to get the ideal seals & gaskets for industrial applications. If you are searching for such a name, then consider getting them from SSP Seals. Being the FDA approved custom industrial seals and gaskets manufacturer, the firm not only offers a wide range of quality sealing solutions but also assure competitive pricing that remains unmatched in the industry. Get in touch with the team and see what best they can offer to seal your industrial applications.
Related Post